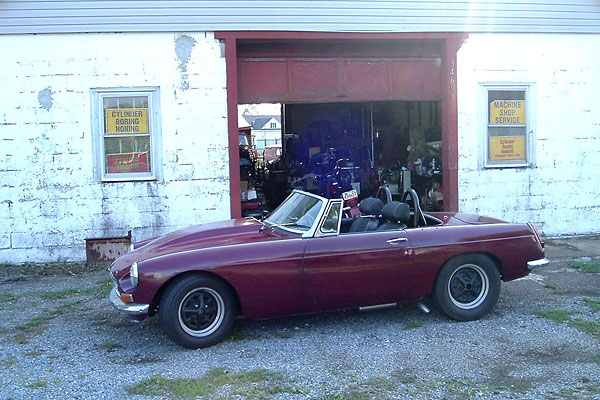
Greg Myer takes us along for an inside look at a few local machine shops!
Machine Shop 101: an introduction to the basic processes
as published in British V8 Newsletter, Volume XV Issue 3, December 2007by: Greg Myer
What happens at a machine shop? What do we need to know before we take our parts to
the machine shop? Does it even matter? Maybe we just want our block bored and to
get on with the build. Well it depends very much on what your goals are, what the
intended use of the engine in question is, how much horsepower you intend on
producing and how long it's designed to last.
The more knowledgeable one is going in, the more intelligent questions you can ask
and then the result should be a better build when you get all your parts back. We
will look at a number of areas starting with some very basic information so you can
see how these things work together. They do work together. Never forget that there
are relationships, many and varied, between all the functioning and nonfunctioning
parts of your motor.
Relationships
No, I'm not going Dr. Phil here. First there are mechanical relationships. Piston to
bore clearance for example measured in thousandths of an inch. Many different dimensions
need to be considered. Some will be built into the new parts and need to be checked and
others will need to be machined to specifications. Other relationships are when things
happen. In engines these are usually measured in degrees of a circle, which has 360º.
Spark timing, for example, might be expressed: in degrees "Before Top Dead Center"
(BTDC). Some of these relationships are affected by the machine work. A third
relationship is ratios. An "over-square" bore to stroke ratio for example. These mostly
fall under the design stage of planning the build rather than the machining process.
Also included in ratios are volumes. Intake port volume and combustion chamber volume
come quickly to mind. These are affected by various machining jobs performed on the head.
Theory and planning will determine the direction of your build. The machine work will
make it possible.
Lets start with the block. We'll use a V8 block for reference. (This is British V8 after
all!) Buick, Rover, Chevy or Ford; doesn't matter to the machinist. We'll talk generic
here as it makes little difference. The block has eight cylinders, composed of two banks
of four in a 90º "V" pattern, as viewed from the front. The crankshaft rides in the
journals at the bottom of the block and the heads are bolted to the "decks" above the
two cylinder banks.
First, you disassemble your engine. If there's little wear on the cylinder walls, and
little or no ridge at the top, pulling the pistons should be easy. If there is a bit
of a ridge, use your ridge reamer to remove it so the piston rings won't get caught.
If it's not worn much, you can use a glaze breaker and just put new rings in it, using
the same pistons. You should thoroughly clean everything and use new bearings, etc.
Look at the lifter bores too. If they're glazed from high mileage you can use a brake
cylinder hone to make a finish that the new lifters will work with better. You are
using new lifters, aren't you? Here's a law: always use new lifters on a new cam. Even
if you have what appears to be a good used cam, you will be miles ahead if you install
new lifters on it. (Besides, lifters are relatively cheap.)
When the bores are worn and new pistons are needed, the bores need to be enlarged.
Pistons come in "oversizes" and the block needs to be bored to match. If the new
pistons are 0.030" inches larger in diameter, then the bore size needs to be
increased by a like amount. The new pistons will come as a matched set. The machinist
needs them in hand to bore your block. He will also need the old ones to press the
old pistons off and the new ones on. This calls for knowledge as the pistons may
have different valve relief notches to match the pattern in the head. Some piston
sets also have the pin bore offset to the thrust side of the engine. Your machinist
will know how all that needs to be put together. The rods should be marked by number
and need to go back together on the crankshaft in the same sequence and same direction.
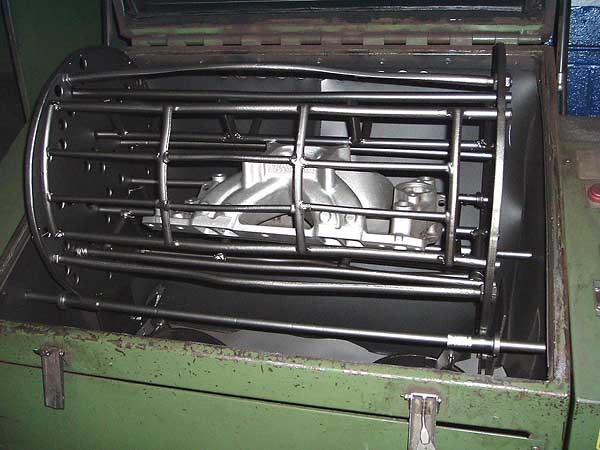
At the shop the block will be inspected and the cam bearings removed, as well as the freeze plugs and galley plugs. Then it's into the cleaning solution. These vary. Hot tank with strong chemicals or a high pressure cleaning using a strong soap that's bio-friendly are two of the most common. (Aluminum can't be hot-tanked!) The cleaning is for more than aesthetics. There will be a build up of crud that needs to be removed from the oil galleys as well as water passages. Since the freeze plugs and pipe plugs will be removed before this process begins, you'll need new ones.
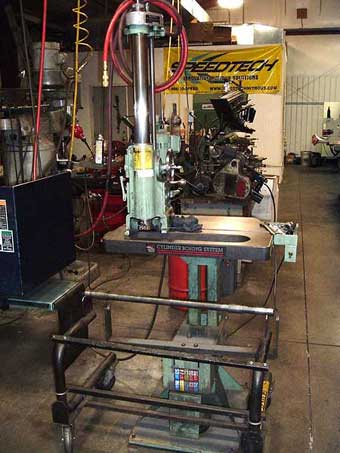
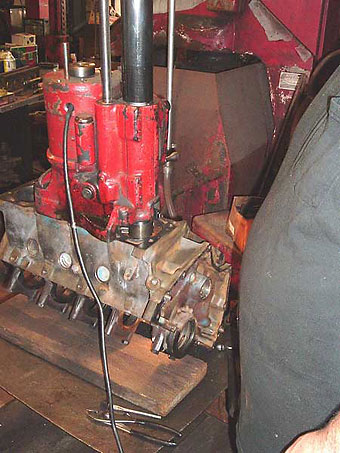
Boring bars vary in design. A small local shop may have what's know as a portable boring
bar, this type is less expensive and it mounts off the block's deck. This is acceptable
if the deck is square and parallel to the crankshaft bore. If, however, the deck is closer
to the crank at the front of the block than the rear, the new bore will start right but
end up angling towards the rear of the block. Bad news! If assembled this way, there may
be excessive loading on the top front of the piston and lower rear skirt as well as the
rods riding on the crank pins. This type of bar is fine as long as the operator does all
the checking he needs to first.
A boring bar that mounts off the crankshaft bore prevents this problem. That's the second
type. It's also known as a portable boring bar. It may not look portable, but the one in
Bill Cannon's Garage was recently taken on board a work boat and used to bore a large
diesel engine. Not an easy task, but less complicated than pulling that motor. There
are many of these types in use around the country. They can provide a good, consistent
job. Again, the operator needs to be familiar with his equipment and make all the checks,
but the boring bit is always at a 90º angle to the crankshaft. That's a good thing!
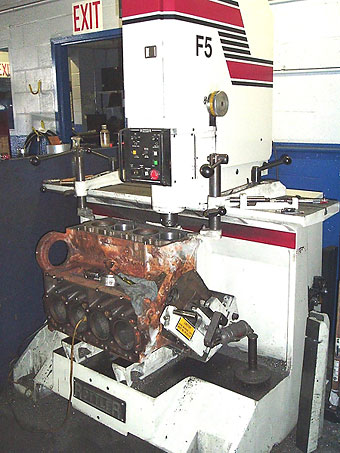
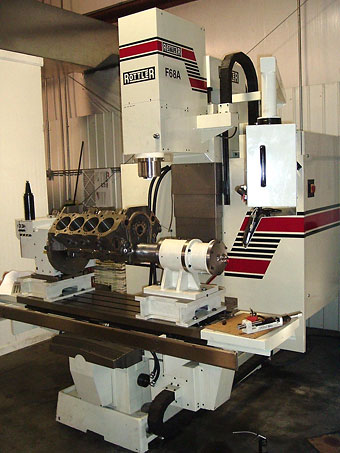
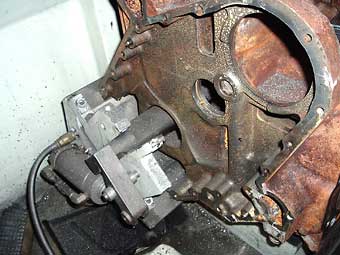
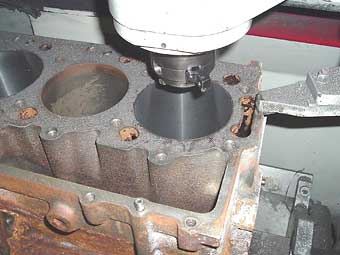
The third type is a boring machine. It's not portable, no matter how large you are.
The Rottler unit at the local NAPA Machine Shop is a good example. These are large
units that are designed for a long life of heavy use. With periodic maintenance and
sharp cutting bits they can do a fine job for many years. These mount the block off
the crank bores too and are quite accurate. This is what most of us can hope to find
in the local machine shop. If that's what you see, you're in good hands.
The fourth type of machine used for boring is a CNC Machine (CNC stands for:
"Computer Numeric Control") and they are state-of-the-art! This is the one that
all the fuss is about. The example in the photo is at Bill Cannon's Awesome Engines.
It's a four-axis, computer-controlled machining center. It can perform a multitude
of tasks, not just bore a block. While it's doing these complex jobs it holds tighter
tolerances than is possible with the other types of equipment. That's great! It's
also a very expensive piece of machinery. It requires software and/or someone very
astute with both computers and machinery to program it. You will understand if the
charges for this type of machine work are above and beyond other, more common shops.
You get what you pay for.
Do you need this amount of accuracy? Well, there's no such thing as being too accurate!
On the other hand, if you're building an average, daily-driver type motor, your local
plain-Jane machine shop will probably work just fine for you, at an affordable cost.
Going racing? Planning to use nitrous or a turbo? You'll need higher dollar parts to
begin with, and top-quality machine work could very easily be exactly what's needed
for all those pieces to live together and retain their performance edge longer.
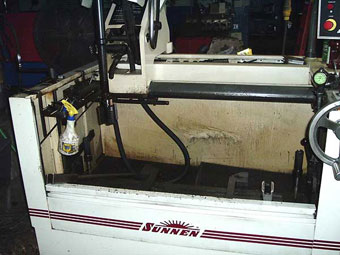
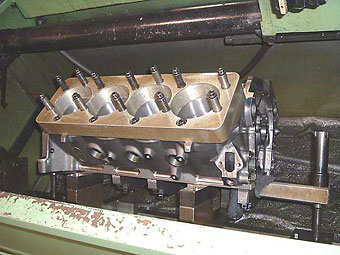
Whichever machine does the boring, it won't open the cylinder all the way up to the specified diameter. Rather, it stops short and a honing machine is then used to take the cylinder to the correct size and crosshatch finish. This is for seating the rings. There are several types of machines to do this task. There are several approaches to the job too. The honing machine at my local NAPA is a good example of what is used in many shops. High performance machine shops carry this operation one step farther by using a deck plate bolted to the deck to simulate the stresses the head will exert on the block after assembly.
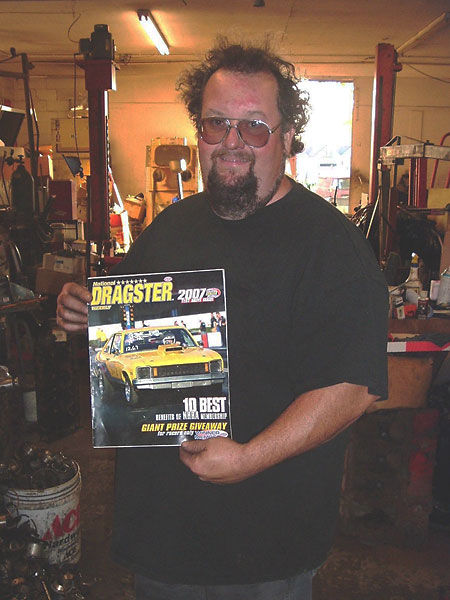
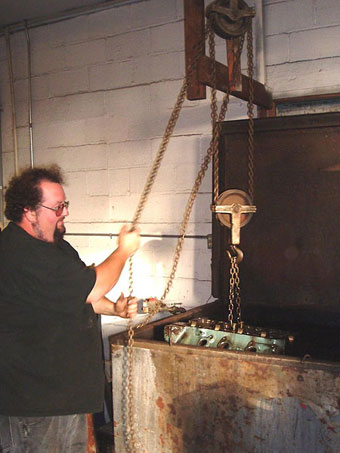
One point we need to understand is that whatever equipment is used, the machinist
needs to be familiar with it and know its proper set-up. My local machine shop is
Bailey's, in Pittsville, MD. The owner, Kevin Bailey, has been a friend of mine for
years. He's done a lot of my machine work and I've done some porting for him. It's
a one man operation, and he gets friends he knows well to help out when needed. The
shop doesn't look like the ones you'd see in the magazines like "Engine Masters" or
"Hot Rod". It might even scare newcomers, if they didn't know what they were looking
at. Don't be put off. It's organized in Kevin's own way... and it works! He knows
what he's doing. In fact he built the engine for the 2006 NHRA Summit Pro Bracket
World Champion, Phillip Truitt of Parsonburg, MD. Things like that don't happen by
accident!
Let's watch him as he performs some routine jobs. First the block is hot-tanked in
a 180º chemical solution. After removing and flushing the chemicals off, the machine
work can start. Kevin sets the block on a work stand and checks it. The deck is
important as the boring machine squares off of it.
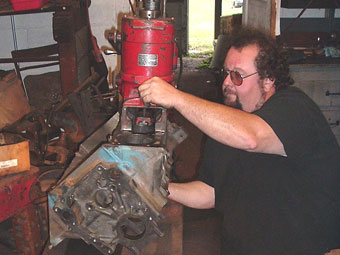
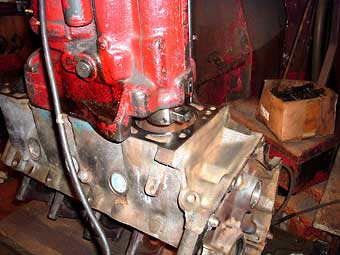
The machine anchors to the main bearings so nothing changes position once the boring
starts. He begins by using a micrometer to set the diamond dressing tool for the
correct diameter. In this case, an Olds 425 that has a stock bore of 4.125" is being
opened up 0.030", so the tool is set for 4.155". In reality it's slightly less as
Kevin will finish the final dimension by power honing.
Often, we read about certain skirt clearances for racing pistons, etc. that sound
like a trick set up. Don't ask for your machinist to give your pistons skirts that
clearance. He can't. The piston skirt clearance is built into the piston. The bore
is for the top of the piston and the rings should match.
Honing
This can vary. In Kevin's shop almost everyone is using Moly rings so he finishes the bore with a 300-400 grit stone in his Sunnen 4 blade hone. The hone has 2 stones and 2 wipers to maintain it square at all times. Honing oil is used for this process.
Enjoying this article? Our magazine is funded through the generous support of readers like you!
To contribute to our operating budget, please click here and follow the instructions.
(Suggested contribution is twenty bucks per year. Feel free to give more!)
Your machine shop will need to know what type of rings you are going to use so they can properly finish the bore surface to make it so the rings seat. This is important. Many racing engines using the latest technology in the ring package need little or no time to seat. They are ready when assembled. For example, the crew at Bill Cannon's Awesome Engines Machine Shop run new engines on the dyno to check how everything functions together for the first time and to run them through a heat cycle to temper the metals. The only problem he's run into recently is with roller lifters. They need oil with zinc in it, and without it they can have problems, which is easy to understand considering the high valve spring pressures that racing profiles need to run.
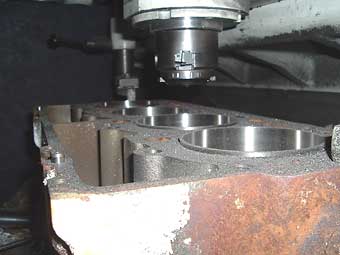
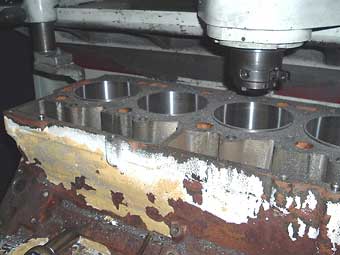
Another phase of the machine work that involves boring and honing is sleeving. If a block has damage to a cylinder wall, it may be able to be saved by boring the cylinder in question oversize so a sleeve can be pressed in. Usually a step or lip is left at the bottom of the bore for the sleeve to butt up against so it can't move. This may differ if the block is aluminum and had sleeves in the first place. Once in, the sleeve needs to be finished to the size of the piston and rings.
Rod Preparation
Back to Kevin's for the next step: the rods. Kevin uses a Sunnen Rod Machine. First,
the old pistons are pressed off the rod. Then the rod is checked to see if the big
end is out-of-round. If needed, it is resized. The bolts are pressed out and the
mating surfaces on both the rod and cap are ground down 0.001" each. The new bolts
are pressed-in and torqued to spec. Then the machine hones the opening to the proper
size. This machine has several mandrels for various applications. Each mandrel uses
one stone and 2 "shoes" for alignment. Rods can have the casting lines ground off
their beams and then polished to reduce stress risers and improve their fatigue life.
Rods can also have the side clearance on the big ends opened slightly. This can be
done on a belt sander. It reduces drag without any oil pressure loss. For stock engines
about 0.010" can be removed when measured with both rods that mount on the same journal
are stacked side by side. For performance motors up to 0.040", measured the same way.
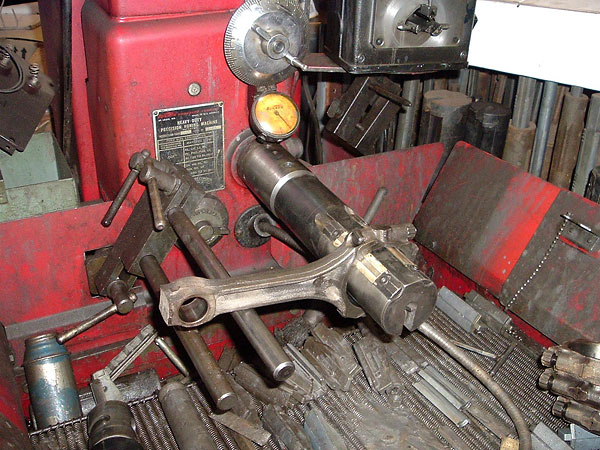
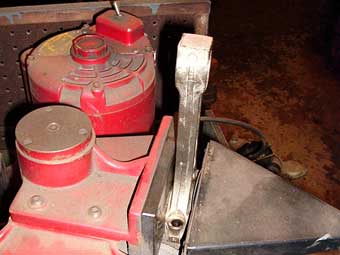
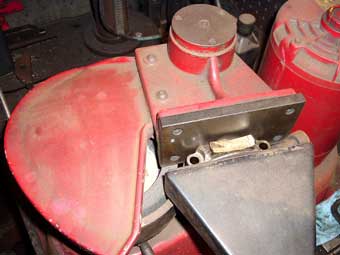
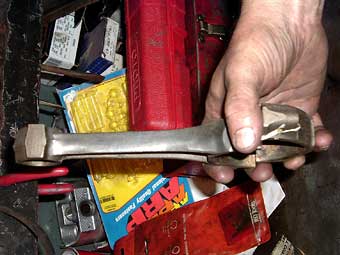
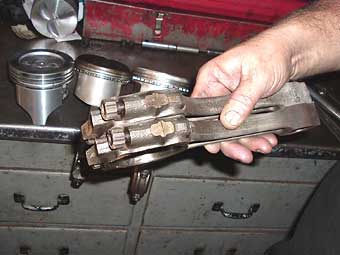
Once they're ready, the small end is put into an oven or heater and warmed up to 1100º. The pin which goes into it has an interference fit. That means it's too small for the hole. When up to temperature Kevin can now mount the piston and pin into the rod by hand. Yes! The pin slides in that easily, and when it is cool, seconds later, it is locked in place.
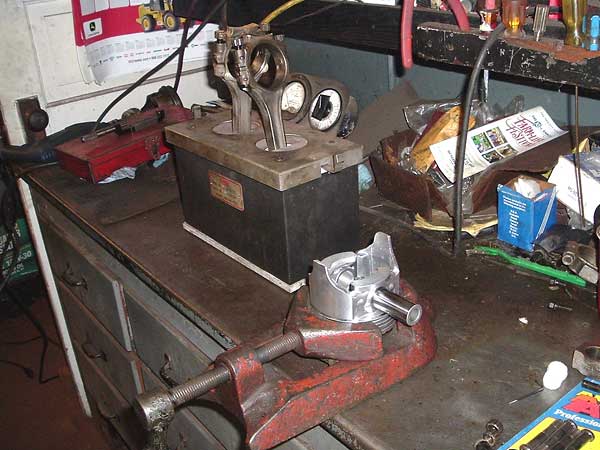
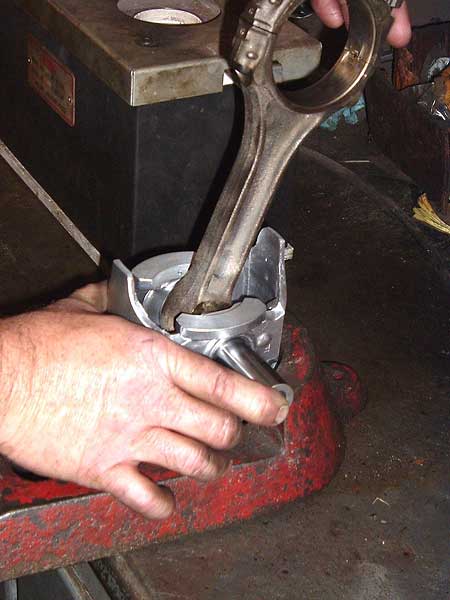
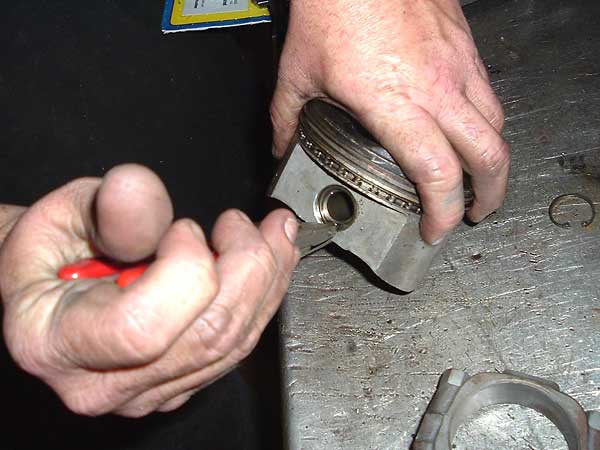
Depending on your piston choice, you may want full floating rods. That's where the pin slides in the rod and uses C-clips, rings, or circlips in grooves in the piston to keep it in place. To do this with press fit rods, the small end needs to be bored to the proper size and bronze bushings with an oil hole are pressed in. After this you could assemble the pistons and rods at home. However, if you decide to try that, please make sure you know what you're doing! The rods have different faces on the sides of the big end. One to mate to another rod and one that's beveled to fit the fillet of the crank throw. Also to be considered is the orientation of the piston. The valve notches, if there are any need to match where the valves are and even if you are using dished pistons, the pin will be offset as the pistons have major and minor thrust sides. Your machinist will mount them correctly. Just make sure you fit them in the correct position when reassembling the engine. (I once bought a set of 'almost new' TRW pistons inexpensively because a young man had put then in the block wrong and bent most of the brand new intake valves in his 302 Chevrolet.)
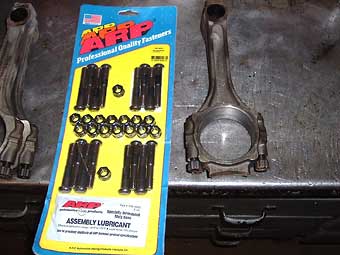
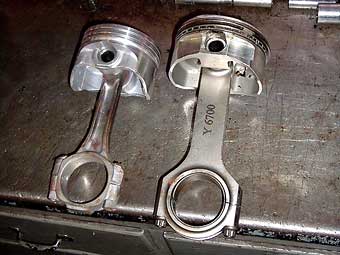
One more important note about the rods: use new bolts! Many times these are overlooked. They can cause very rapid destruction of the crank if they fail. One long time drag racer I knew said he never saw a rod bolt break. Well, they do break, but mostly they fatigue and stretch. Then what? The clearance on that rod bearing opens up. More oil rushes past and oil pressure drops. That's the first sign of trouble. It won't last long as the rod bearing will soon spin because there isn't enough crush to hold it in place. The crank and rod will be destroyed very swiftly thereafter. If the rod breaks, it can hole the block. Stock replacement bolts are better than old fatigued ones, and aren't too pricey. There are many others to choose from too, and no matter what the cost, it's cheap insurance in the long run.
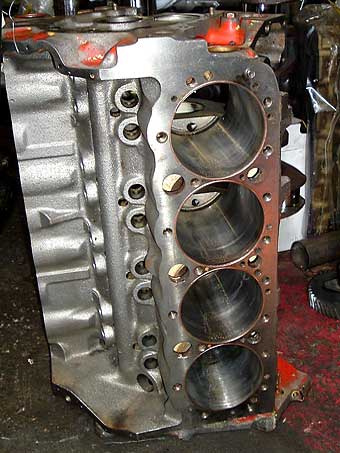
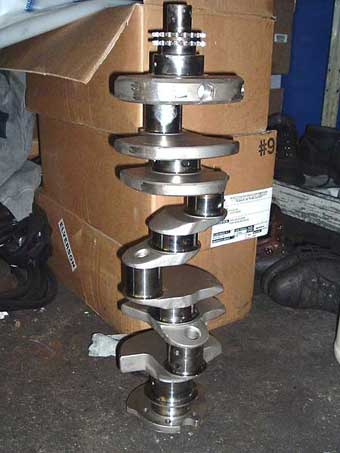
Other Machining Processes
There are other things to consider while the block is undergoing its surgery.
How about grooves for o-rings in the deck? Depending on the compression you
plan to run, or if a turbo or nitrous is to be used, it may be a very important
step. Turbos and nitrous oxide use create extreme cylinder pressures and can
overpower the head gasket if everything isn't exactly right. O-Ringing the block
(or head in some cases) and using the proper gasket, and following the
manufacturer's recommended torque specs and sequence can go a long way to
keeping the motor together.
While we are discussing the deck, there a few points to note. If, for example,
the block needs one or more sleeves, or there was warping or for some other
reason the deck was in question, it will need resurfacing. (This is also the
case when you want to "Zero Deck" your motor during the build.)
Usually, with most cast iron blocks, the machine shop is all set to "shave" the
deck. They've done it often and know what's needed. However, with some aluminum
blocks, using either iron or aluminum heads, and many late motors, there are
special considerations. Check the instructions on the headgasket! You may find
that a certain roughness average (Ra) in microinches is specified. The old "iron
block, iron head" combination with a composition soft-face gasket needs 60 - 120
microinches Ra, while an aluminum head on iron block with the same type of gasket
calls for 20 - 50 microinches Ra. Some newer OEM engines with multilayer steel
head gaskets require even smoother finishes (perhaps 20 - 30 microinches Ra) and
there are even a few that recomend 7 - 15 microinches Ra. Check with the
manufacturer before scheduling the work. Do not assume the shop knows what type
of gasket you are going to use.
New cam bearings will be driven into their respective positions. If you've seen
a cam bearing driver and are tempted to try it yourself, remember; the bearings
get smaller as they go from front to the back of the block. The size difference
isn't great so you need to pay attention or you could damage one. Also, I like
to 'clock' the bearings. That is rotate them in reference to the bottom of the
block. Looking at the cam from the front of the block, I like the oil holes at
about 4 o'clock. That way the oil is heaviest where the pressure is the greatest
on the bearing.
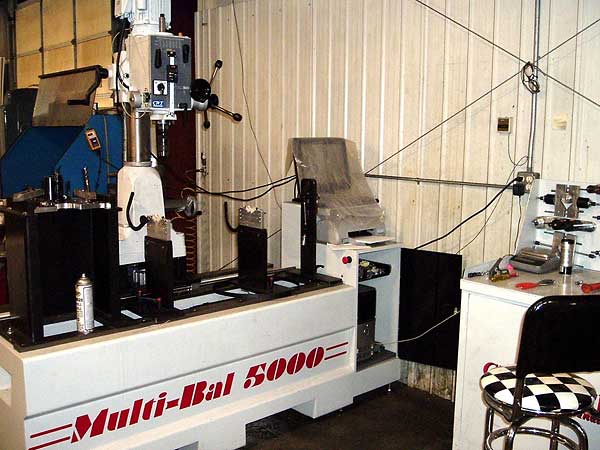
Balancing is something that needs to be done here too. New pistons weigh a bit
different than the old ones. That calls for changes somewhere. Resizing the rods
changes their weight too. All of the pieces need to be weighed individually, and
matched to the lightest in the set by removing material. The crank is then spun
with bob weights on the rod journals that equal the combined weight of the rods
and pistons to determine how much needs to be added or removed from the crank
throws. Removing weight is done by drilling. Adding weight requires putting a
heavy metal ("Malory metal" is denser than steel) in the throws. This is a critical
step for high-revving engines, whereas components that are similar-to-stock put
into a stock motor may not always need balancing. Ask your machinist if you have
any questions.
Align boring is when the main caps are treated in a similar fashion as the rod
caps were. Material is removed from the mating surfaces and then the caps are
torqued in place and bored the length of the engine, assuring a straight seat
for your crankshaft. This has to be done if you bought a new set of 4-bolt main
caps for your 2-bolt block. The other 2 bolt holes will need to be bored and
tapped on each cap at this time too.
Crankshafts are part of this shortblock package that we've been discussing. The
machine shop can check yours for straightness, and straighten it if necessary.
The main and/or rod journals may have wear and need to be turned undersize. When
that is done most shops supply the properly sized bearings when the crank is
returned. Polishing the journals will help it move smoothly on the oil film layer
between the crank and bearing. Getting the crank "indexed" can be helpful with
some factory cranks. That's where all the throws are checked and offset ground
as needed to be 90º or 180º from the others. I know, that's the way they should
come from the factory, but it ain't necessarily so. If the throws are off by a
few degrees, well, there all sorts of relationships will be messed up too!
Where will the piston be when the intake valve opens or the plug fires at what's
supposed to be 36º BTC at 5500 RPM? What effect will it have on exhaust scavenging
if the piston is several degrees late getting to TDC compared to camshaft events?
Go ahead Dr. Phil, just try to answer that one.
That about wraps up the machine work on the short block. Oh, there are other things
that can be done, but this is just to cover the basics. If you want to get even
deeper into machine work and engine building, you might like to check out some
of the books or magazines out there that specialize in just that.
Editor's note: We would like to thank Bailey's Machine Shop, on Main Street
in Pittsville Maryland (phone 410-835-2241) for their help with this article.
Disclaimer: This page was researched and written by Greg Myer. Views expressed are those of the author, and are provided without warrantee or guarantee. Apply at your own risk.
Photos by Greg Myer for The British V8 Newsletter. All rights reserved.