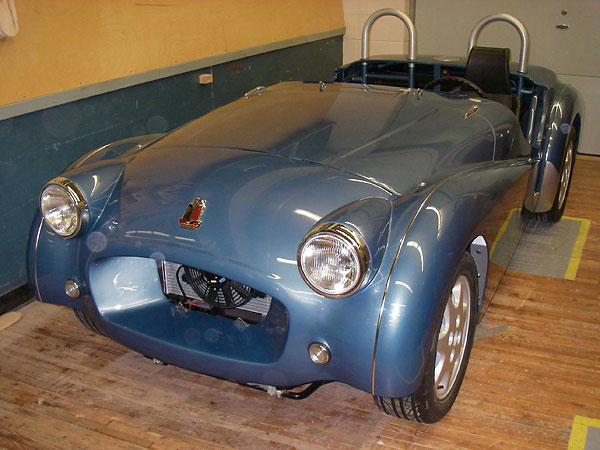
Randy Schultz's Triumph TR3 "Plus 4" Project, Part 1
as published in British V8 Magazine, Volume XVI Issue 1, May 2008
by: Randall Schultz
The inspiration to undertake this conversion came from a simple idea:
"Use the Triumph parts I like, don't use the Triumph parts I don't like,
and use parts from other cars to produce the ultimate TR3." For me, the
classic early TR3 body was the strongest styling statement Triumph ever
made. It defined the spirit of British sport motoring. The TR6 chassis
represents Triumph's highest development of the body-on-frame concept,
featuring independent rear suspension as well as rack and pinion steering.
My intention was to produce a vehicle that captured the essence of the
TR3, except with better handling, brakes, and engine. I also wanted modern
reliability and the ability to get service parts anywhere. From my point
of view, none of the Triumph engines or electrical systems would be
suitable for the project.
A TR3 body doesn't fit on a TR6 chassis. The TR3 body is narrowest just
behind its doors - just where the TR6 chassis is its widest! (This
corresponds to the outboard side of the rear trailing arms of the TR6
independent rear suspension.) Even with careful cutting and re-definition
of the back end of the inner sill boxes, the body still needs to be at
least four inches wider to fit the TR6 chassis.
I took my lead from famous auto designer Alec Issigonis, the man behind
the Morris Minor (and most famously the classic Mini). History documents
the development and final design of the Morris Minor as a derivative of
the Mosquito. Issigonis at the last minute, and in a flash of inspiration,
had the Mosquito cut in half lengthwise right up the middle and added
four inches! If you look at the roofline on a Morris Minor you can see
the gentle curve of the roof very nearly becoming flat in the center
four inches.
The great thing about history is we can learn from it. I can cut a car
in half too. With the silent blessing of Alec Issigonis, and the number
four as the guiding light to glory, I proceeded to "bastardize a
perfectly good car".
The patient for my surgical procedure was a straight and rust-free
1958 Triumph TR3 from California. Some would say my actions are nothing
to be proud of. However, I show no remorse, and stand behind my work as
the only thing that could have been done to build the ultimate TR3. I'll
admit there was a moment or two just before "the procedure" where I stood,
zip-disc in hand, wondering if I were completely insane. Once the first
incision was made, it was all business. I have never looked back or
regretted my decision.
I do as much work as I can myself. I am well versed in traditional
bodywork techniques, and prefer to do things the way the old guys used to.
For me, every job is a wonderful journey through fields I enjoy walking.
When people ask me "Don't you just want to get it done and go driving,"
I can honestly reply that the journey interests me more than the destination.
I enjoy the process as much as the product.
I logged 681 hours of sheet metal work in this project. That includes all
the cutting, widening and general fabrication of the body. For bodywork, I
used oxyacetylene gas welding exclusively. Specifically, I used the
traditional technique of butt hammer-welding with no filler rod to produce
light-tight joints. This requires simple tools: a size "000" torch tip and
a good hammer and dolly. If anyone wants to know more about this realm,
just ask me about it.
Steel filler strips were added, of course, right up the centerline of the body and even through the dashboard. Each filler strip matched the profile to its right and left in all respects including curvature, bends, ribs, etc. From the hood rearward, the strips were four inches wide, but forward of the hood I decided to add only three inches along centerline, and to add a half inch along each side. [Editor's note: It's hard to see in the photos, but this added steel is just inboard of the fender seam. It's about two inches outboard of the headlights.] Because the hood itself was widened by four inches right up its middle, some re-contouring of both hood and nose was required to bring curves and edges into alignment.
Enjoying this article? Our magazine is funded through the generous support of readers like you!
To contribute to our operating budget, please click here and follow the instructions.
(Suggested contribution is twenty bucks per year. Feel free to give more!)
I used an extra trunk lid to fill-in the bodywork behind the seats. I feel this space is useless for the original advertised function of occasional seating. As well, it offers no security for cargo storage. By closing this in, I was able to reverse the fuel tank and gain nearly a foot of trunk space. Rollover protection hoops project through this deck and I decided to relocate the fuel filler to this area too. The roll hoops also have brace tubes on either side of the car running from the front floor pan frame mounts, over the rear wheel arches, and into the trunk where they ties into the floor at the back. This system forms sort of a truss arrangement that really adds rigidity to the body.
The fuel filler door is a Ford Mustang aftermarket part, with the Ford
logo carefully filed-off the inside of the lid. The filler cap lives below
this and is the original Nissan part connected to the TR3 tank. Since I'll
be using aftermarket gauges the original Triumph fuel sender (resistance
range = 0-9 Ohms) was discarded in lieu of a VDO universal fuel level sender.
Turning attention to the chassis... I welded-over all Triumph's original
frame welds. In comparison to the earlier TR3 frames, the TR6 welds are
much poorer. Almost all of them were "cold". After sorting this out, the
frame was sent off for powder coating.
The running gear is from a 1991 Nissan 240SX. The engine is a 2.4 liter,
16-valve OHC electronic fuel-injected design with about 168 HP through the
"SX" 5-speed box and limited slip differential. That's about a 68% increase
in power over the original Massy-Fergusson tractor derived power plant that
used to pull the TR3 around. One of the founding concepts in this project was
to run clean with good power, reliability and economy. The engine has full
emission control features including catalytic converter, O2 sensors, etc.
included in the installation.
To keep the power reliable at the stern, I used Corvair spindles running
in custom-built hubs. This isn't a new idea. Back in the day, Corvair or
Mercedes spindles were commonly used on racing Triumphs because the TR6
axles would break due to poor design. (The TR6 axle ends conclude in a long
taper with a keyway cut along that taper. When free-play develops between
the axle and the hub assembly, the axles break as the hardened key impacts
its way to victory over the softer axle material.) There is a U-joint that
will connect the Corvair yoke to the TR6 yoke, thank God. The inside of the
trailing arms needed some slight relieving, but it all worked out neat in
the end.
The Nissan differential is the limited slip unit referred to as the "R200".
After looking at Goodparts' conversion kit to mount the differential to the
TR6 chassis, I decided to make my own. The Nissan driveshaft assembly was
shortened to match the new driveline length. Other rear modifications
include a tube shock conversion located within the spring, as well as a
custom sway bar mounted from above. I have fitted in the Goodparts rear
camber adjustment system between the frame and trailing arms to be able to
flaunt how much rear camber the ultimate TR3 can have.
The engine sits very well in the new engine bay with no interference issues
with steering, exhaust, firewall etc. I made custom frame brackets to mount
the engine and was able to use the stock Nissan mounts.
The engine oil pan was, however, an issue. The Nissan 240SX has a front sump oil pan and I needed a rear sump to clear the front frame cross-member. I thought this would be easy, as the same engine was used in Nissan trucks like the Frontier with a reversed pan. However, in truck applications the front timing-chain cover is a different shape and this forms the front edge of the pan shape. I used both pan types, taking the original front sump, cutting it down and grafting it to the back half of the truck pan. I re-routed the oil pick-up to the back using a variety of piping from both set-ups welded into the correct shape.
The radiator is an all aluminum, three-row core, cross flow unit, for VW racing applications from Summit Racing. The (pusher) fan set-up is from Perma-cool. Exhaust manifold is stock, except for the removal of casting marks and the standoff bosses that the original heat shield bolted to. I had the manifold ceramic coated, with the effect of reducing the running temperature of this part by 300 degrees (and because it looks cool!)
The front brakes feature Toyota 4-runner four piston calipers and Toyota
Cressida vented rotors. Nissan 240SX discs were installed in the rear. The
Toyota 4-runner calipers literally bolt right on with no modifications. Fitting the
Cressida rotors required that the TR3 hub's outer shoulder be machined smaller
by about 0.020".
Because I'm running four-wheel discs, I needed power assist. The smallest brake
booster I found was from a Suzuki Swift. I connected this to a Mazda Miata master
cylinder. (You should use a master cylinder designed for four-wheel discs if
that's what you're running.) To keep the same mechanical pedal ratio of the
Miata, I had to design and build a double-acting swing mechanism to work with
the TR pedal position. This linkage allows longer lengths, without changing the
original ratio. A proportioning valve allows adjustable braking bias between
front and rear.
The 15" alloy wheels are from an early Nissan 240SX. I bead-blasted the
anodizing off, welded-up some curbing mishaps from previous owners, and had
them powder-coated. To get my wheel offsets where I wanted them, I machined
front and rear spacers. The front spacer is 1-1/8" thick and the rear is 3/4"
thick. The wheels are wearing Yokohama "S Drive" 195/55-R15 tires. Ultimately,
I think I'll go the plus one route to fill in the wheel wells a bit more.
The only Lucas electrical components left on the car are lamp housings and
the windshield wiper motor. The wiper system's worm-gear drive (with spacer
tubes that can be cut down, lengthened, or even replaced with 3/8" brake line)
is ideal for being able to move the gearbox units four inches further apart.
My friend who understands the shortcomings of British electrical systems tells
me this is where the fire will start in my car!
The steering column is from a TR6, with a modified outer column tube to get
the right length, and also to eliminate the column-mounted turn signal and
light switches. The car will use the original TR3 center unit modified to fit
on the TR6 steering wheel. The seats are from a Porsche 914. It's hard to
find a good seat that's narrow enough for these cars - even if you've added
four inches! (Actually, I re-designed the transmission tunnel and driveshaft
cover to be a structural part of the body, so it is taller and slightly wider
than the stock arrangement.)
This project is not completed. I still have hundreds of details to address.
Each feature of the design begins with thought and reflection, followed by
pencil sketches, measurements, and in some cases full-scale mock-ups,
templates etc. As each new detail is completed, the car seems to reveal
another aspect of the whole almost as if the detail were there all along -
hidden from view. The resulting car is part vision, part inspiration and a
lot of work! I hope you like it.
This article is part one of a two-part series! If you enjoyed this article, you'll enjoy the sequel:
Randy Schultz's Triumph TR3 "Plus 4" Project, Part 2
A summary of the car's features and specifications appears here:
How It Was Done: Randy Schultz's Triumph TR3
Photos by Randall Schultz for the British V8 Newsletter. All rights reserved.